Real estate is one of the hardest open problems in scaled self driving
Why parking & charging will become the limiting factor to bringing autonomous driving to the masses
I’ve had a minor obsession with Waymo’s autonomous vehicle depots recently.
Over the past few months, I’ve flown a drone as part of a stakeout to understand how they work. And I’ve taken a deep dive into an apparent Waymo outage to find the company charging its electric vehicles from temporary diesel generators.
The reason for my obsession? I believe depot buildouts will be one of the last hard problems in scaled autonomous driving. Long after the hardware, software, and AI have been perfected, real estate acquisition will remain a limiting factor in large-scale AV deployment.
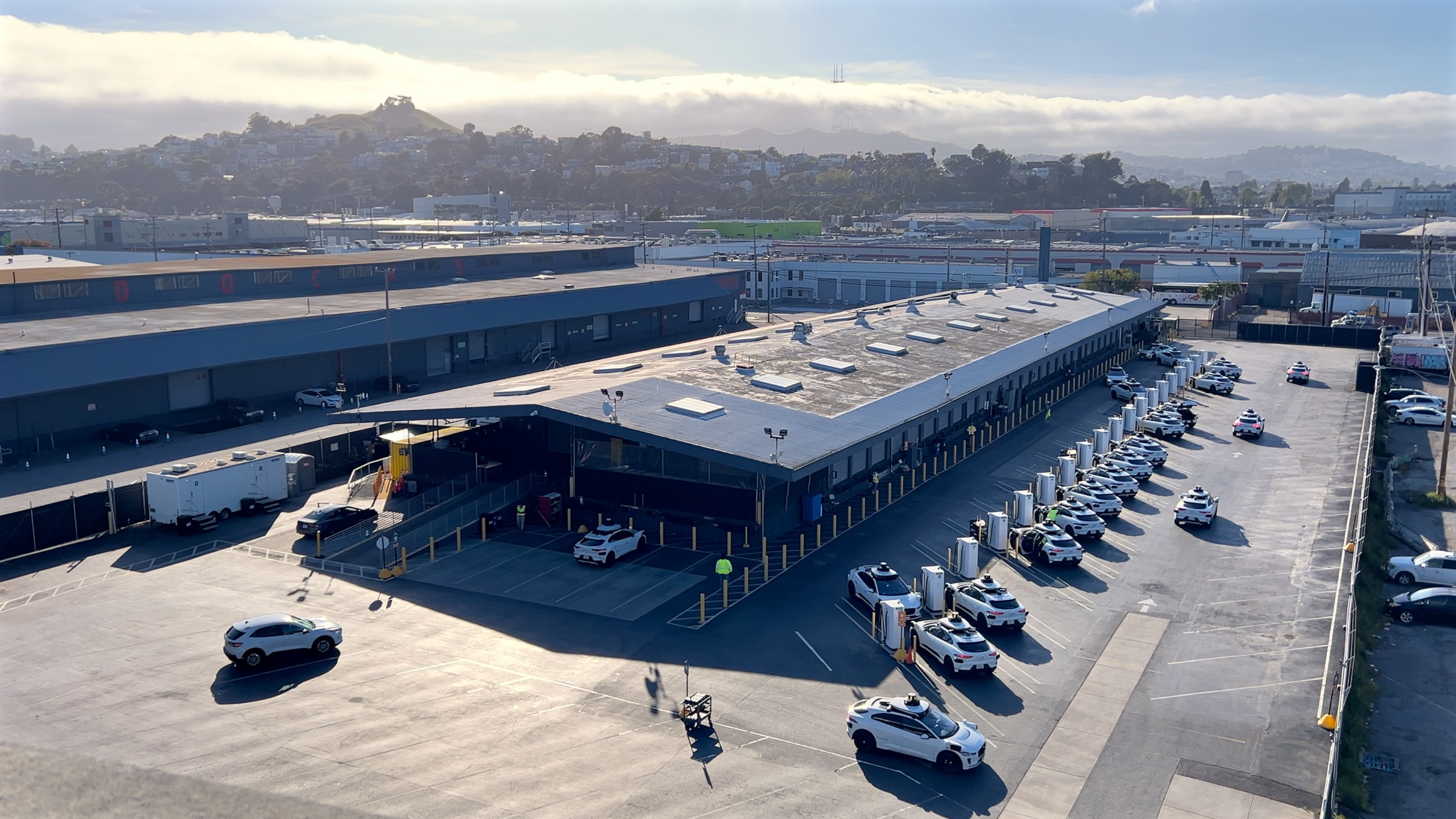
Waymo’s main depot at 201 Toland Street, San Francisco.
Will self driving follow software scaling laws?
In 2021, Elon Musk claimed that Tesla FSD’s release will be “one of the biggest asset value increases in history.”
The day FSD goes to wide release will be one of the biggest asset value increases in history
— Elon Musk (@elonmusk) October 20, 2021
Musk is arguing that, once autonomous driving has been solved, it can be instantly rolled out at the push of a button. Nearly all of Tesla’s fleet could be put to productive use without humans behind the wheel.
While Musk’s viewpoint is on the extreme end, it’s a sentiment shared by many who have worked on or invested in autonomous driving over the years. Once you have hardware capable of supporting safe driverless operation, it’s just a matter of developing the right software. Software can be replicated infinitely at zero marginal cost. Could autonomous driving therefore scale as quickly as software platforms like Uber or DoorDash?
The answer is not so simple. Self-driving cars are still cars — cars that exist in the physical world and need to be parked, fueled, cleaned, and repaired. Uber and other multi-sided marketplace platforms have been able to grow exponentially because they distribute these responsibilities to the individual drivers — many Uber drivers park at their own homes — allowing the platform provider to focus on developing the software pieces.
So far, AV companies like Waymo and Cruise have taken a different approach. They’ve preferred to centralize these operational tasks in large depots staffed with their own personnel. This is because AV technology is still maturing and cannot be easily productized in the short term. Additionally, Timothy B. Lee notes in Understanding AI that “having hardware, software, and support services all under one roof makes it easier for Waymo to experiment with different technologies and business models.” When the kinks are still being worked out, it is more straightforward to vertically integrate everything in a single organization.
The many jobs to be done of a robotaxi depot
Depots for human-driven fleets, such as rental cars or delivery vans, only require a parking area with minimal additional infrastructure. This enables a fairly straightforward trade-off between location and cost: the fleet operator seeks a location close to customer demand while minimizing rent. For example, a logistics company participating in Amazon’s Delivery Service Partner program can run its depot from any sufficiently cheap parking lot near the local Amazon warehouse.
The same constraints affect depot selection for autonomous vehicles. However, the depot also needs to be more than just a convenient parking lot to store off-duty cars.
- Because AVs are often also EVs, the ideal site also has electric vehicle charging.
- Because AVs need to upload driving logs to the cloud, it should have a high-speed Internet connection too.
Let’s explore these constraints in detail.
Location
Depots should be placed close to customer demand to minimize deadheading (non-revenue driving), which would raise costs while degrading the customer experience with longer pickup times. Ideal depots are therefore located in desirable residential or commercial areas, where there is more competition among potential tenants.
Placing depots in high-demand neighborhoods instead of industrial areas can also increase the probability of local opposition. Waymo has already encountered opposition during a proposed expansion of their main depot, even though it is located in an industrial neighborhood with many similar facilities. Again from Timothy B. Lee:
Waymo sought a permit to convert the warehouse next door into some office space and a parking lot for Waymo employees. San Francisco’s Board of Supervisors unanimously rejected Waymo’s application.
The rejection was partly based on fears that Waymo would eventually use the space to launch a delivery service in the city (Waymo hasn’t announced any plans to do this so far). But it also reflected city leaders’ frustration with their general lack of power over Waymo.
Now consider the recent incident in which driverless Waymo vehicles honked at each other while entering a depot near residential buildings in San Francisco, often well into the early hours of the morning. While residents and the company resolved the situation amicably, it will surely be raised in future discussions of new Waymo depots in residential areas should they come before the Board of Supervisors or Planning Commission.
Electric vehicle charging
AV developers have preferred to run their services with electric vehicles. Although AV and EV technologies are not inherently coupled, running a fully electric fleet adds an environmental angle to the AV sales pitch, allowing the companies to claim that AV rides reduce emissions by displacing gas-powered driving. An EV fleet also lowers vehicle maintenance costs.
Waymo and Cruise each have locations with DC fast charging capability. This approach avoids relying on public chargers. Taking Waymo’s primary San Francisco depot as an example, the company installed 38 chargers of approximately 60 kW each, implying a total site power of around 2.4 MW.
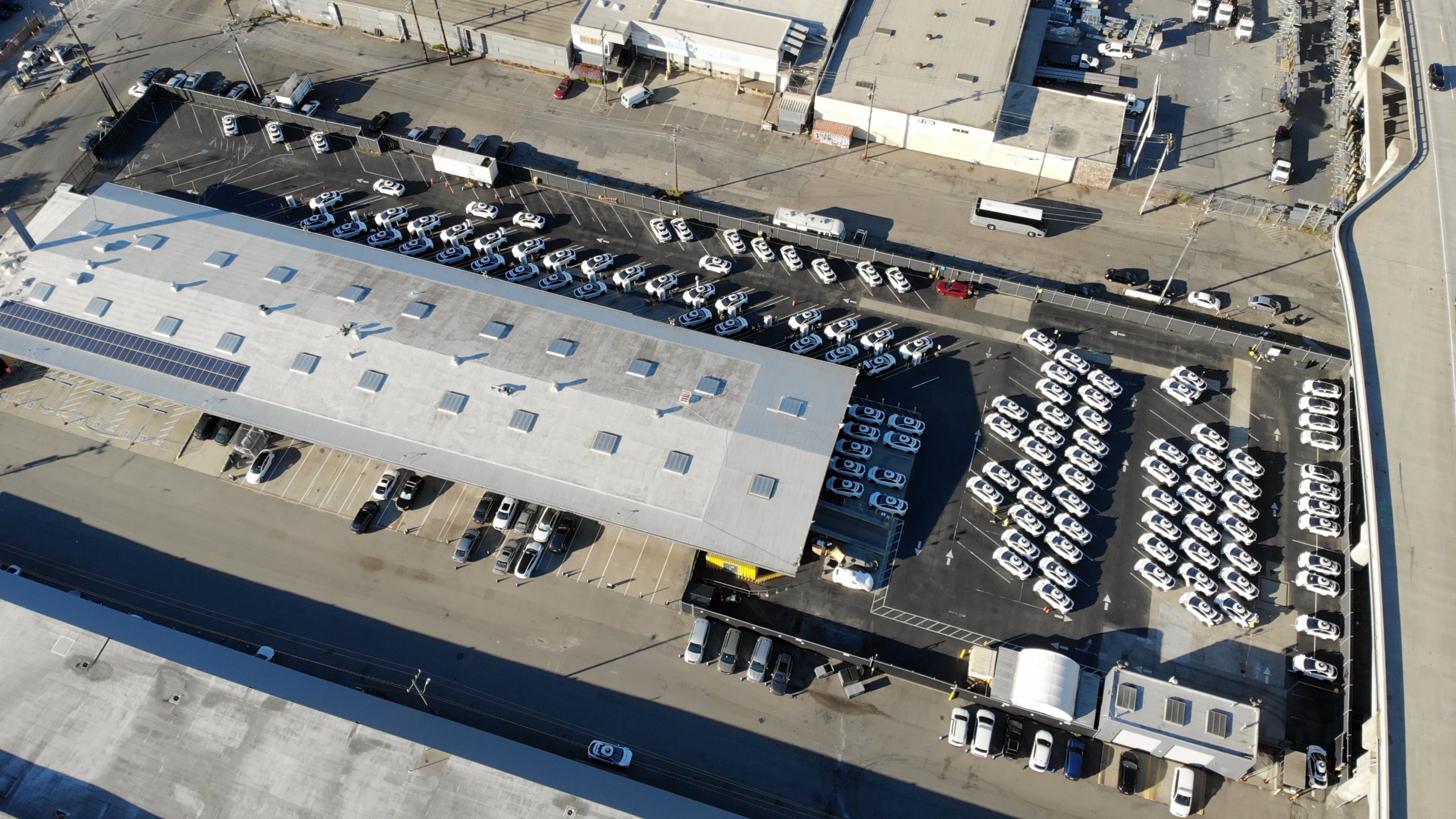
Waymo vehicles charging in San Francisco. Approximately one-third of parking spots in the main depot have charging.
Bringing in so many high-power chargers likely added significant complexity to Waymo’s depot construction. While we don’t know Waymo’s process, we have a fairly good benchmark from the Tesla community, which tracks Tesla Supercharger installations closely. From Bruce Mah, a seasoned EV charging observer, the construction process is:
As with any construction project, things usually start with selecting a site and permitting. There will often be some demolition / excavation of part of a parking lot (Superchargers are often built in existing parking lots). Tesla equipment such as charging cabinets, posts, etc. will usually be installed next (see T1 below). Eventually there will be some inspections from the local Authority Having Jurisdiction (AHJ). A utility transformer (from PG&E, SCE, etc.) is usually the last piece of equipment to be installed. Repaving, painting, and installation of parking stops will also usually happen late in the process, as well as landscaping and lighting enhancements.
Of these steps, permitting and utility work are not within the charging operator’s control. California municipalities, especially San Francisco, have a notoriously slow and political permitting process. With PG&E, the utility serving much of the state, electrical service upgrades involving a new distribution transformer can take months.
Timelines aside, building out a charging site is also expensive. For example, an agreement between Tesla and the City of West Hollywood values an eight-plug location at $482,942 for both equipment and construction.
Data offload
The final piece of the puzzle is data offload. Autonomous vehicles log vast amounts of data as they drive, measured in hundreds of GBs to TBs per hour.
- Some of the data is subject to mandatory retention and must be uploaded for later review. At a minimum, all AV collisions in California must be reported to the DMV. Regulators at all levels of government expect the AV developer to present analyses of serious incidents, including recordings from the vehicle and explanations of the AV’s decisions.
- In addition to regulatory requirements, the AV developer often wants to return much more data for engineering purposes: near misses, stuck events, novel or interesting scenarios, and more.
The upshot is that the AV operator needs to upload a substantial portion of the hundreds of GBs to TBs logged per hour of driving. Uploading over cellular networks would not be cost effective. These transfers must occur at a depot.
Today, it’s likely that Waymo and Cruise use disk swapping for data offload. When a car fills up its internal logging disk, it notifies an operator to plug in a fresh one. The full disks may be uploaded directly from the depot or shipped to a datacenter. This whole process is labor intensive and, over time, may pose a reliability concern due to dust or water ingress.
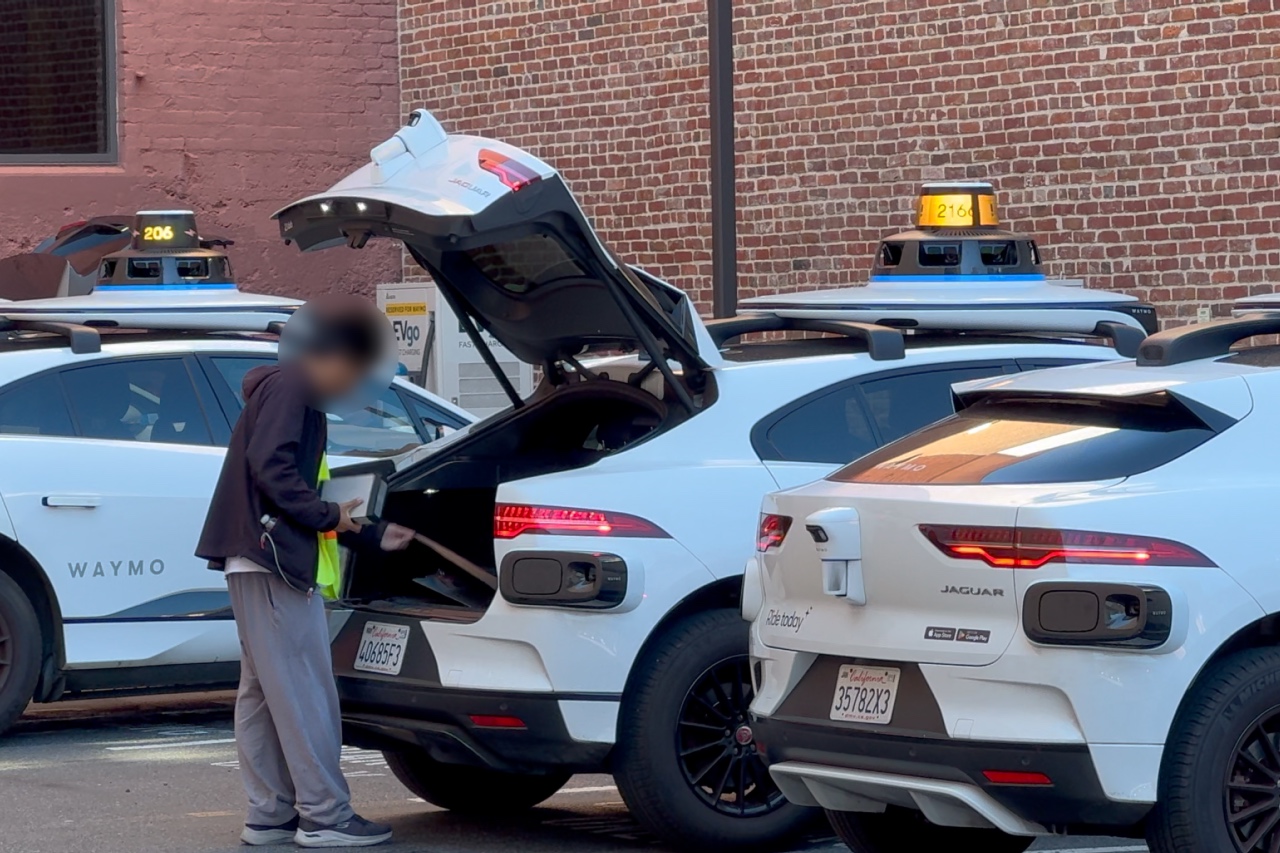
A Waymo operator performs a possible disk swap.
Many AV developers are moving toward direct data transfer from the vehicle using Ethernet, Wi-Fi, or a private 5G network, which reduces the number of manual touch points and moving parts. Charging is a great time to perform these transfers. However, this imposes an additional requirement on the depot: a fast upload speed, probably a fiber connection of at least 10 Gbps.
Where do we go from here?
When we put all three requirements together (great location, high-power EV charging, and high-speed Internet), there may be few to none sites that fit the bill. This would require the AV operator to take on site-specific construction projects to add amenities like charging and Internet — a strategy that sits in direct opposition to rapid and cost-effective scaling.
Another possibility is to engineer ways to relax the constraints.
Decoupling the requirements
Waymo and Cruise do not require all of their locations to have charging and data offload. For example, Waymo operates satellite lots in downtown San Francisco only for storing their off-hail vehicles. Every night, fleet management software instructs the cars to travel back to the main depot for charging and data offload.
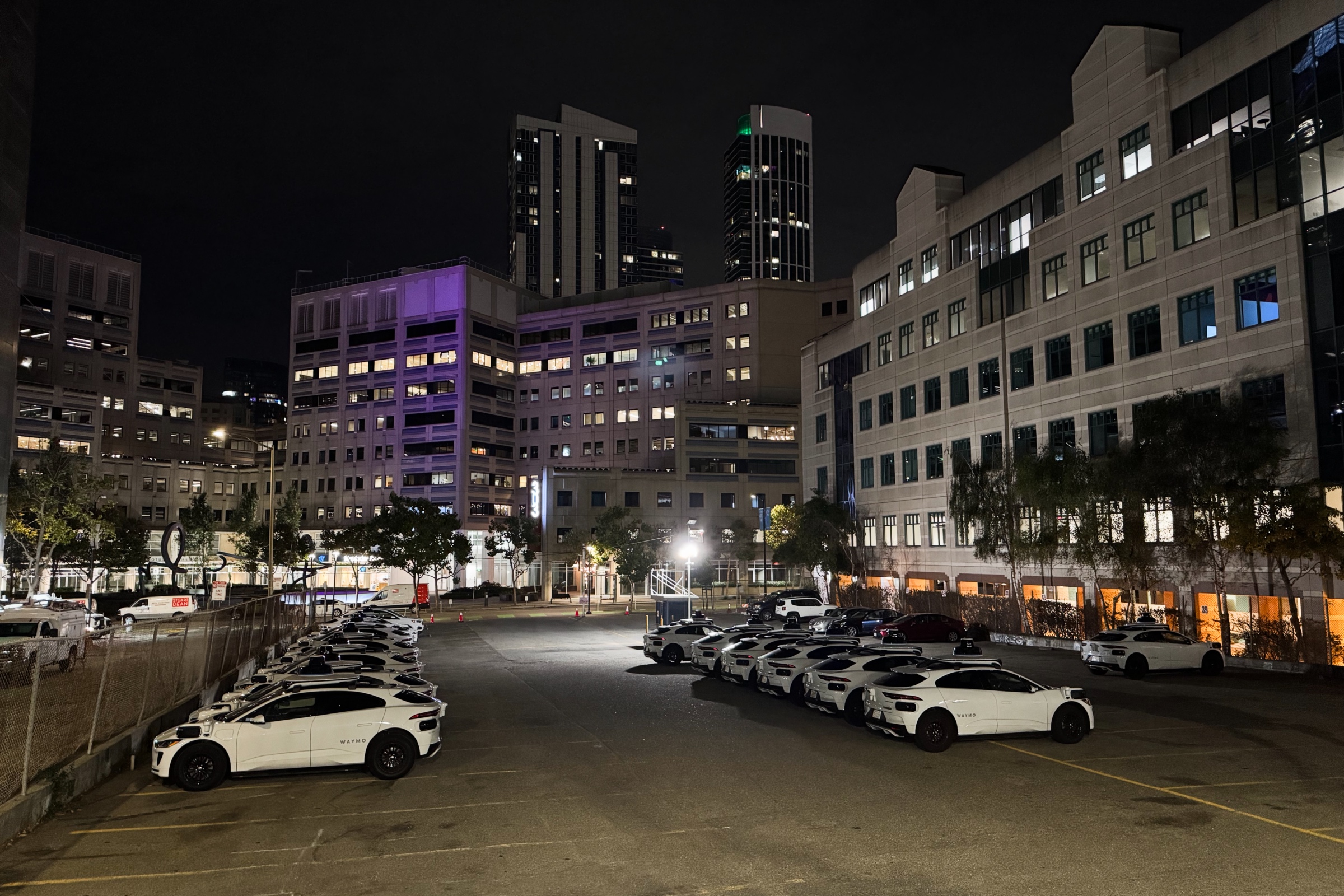
A Waymo satellite location in San Francisco with minimal staffing, no charging, and apparently no data offloading.
This solution works as long as the total charging and data transfer capacity across all locations exceeds the average throughput required to keep the fleet in working order. However, the lack of redundancy can lead to cascading failures, such as the apparent power outage at Waymo’s main depot that led the company to shut down many vehicles during a Friday evening rush hour.
Reducing charging power
Waymo and Cruise currently use DC fast charging (DCFC) for their fleets. Level 2 (L2, also known as AC) charging could reduce the cost of buildouts because the equipment is cheaper and can often be installed without bringing in a new utility transformer. This could enable overnight charging in satellite locations that do not currently have any charging capacity. Imagine an operator arriving at night to plug in all the cars when there is little demand, then returning in the morning to unplug them before customers wake up.
There is an order of magnitude speed difference between L2 and DCFC.
- This is important for consumer charging, where the consumer cares about the time to get a single car back on the road.
- However, charging power for any individual car becomes less important when charging a large fleet. Fleet operators care about the total throughput of turning around cars, which is proportional to total power delivered across all chargers.
In other words, assuming an autonomous ride hailing service will always have overnight lulls in demand and enough parking spots during those times, the most scalable strategy is to procure your desired total charging power at the lowest price.
DCFC equipment costs disproportionately more per kW due to the additional complexity of the charging equipment — and that doesn’t include the additional maintenance complexity. The table below compares ChargePoint’s cheapest L2 and DCFC units:
Charger | Power (kW) | Price ($) | Unit Price ($/kW) |
---|---|---|---|
ChargePoint CPF50 | 9.6 kW | $1,299 | $135/kW |
ChargePoint CPE250 | 62.5 kW | $52,000 | $832/kW |
In addition to more scalable depot buildouts, reduced charging power can also improve the longevity of the vehicle’s traction battery, which is an important factor in managing vehicle depreciation.
Reducing data logging rate
Most AV developers start out by logging and uploading all data generated on their vehicles. This makes development easy because the data is always there when you need it. These assumptions need to be broken when a growing fleet generates proportionally more log data, most of which contain routine driving and are not very interesting.
We can split the data logged by AVs into two categories:
- Raw sensor data, such as lidar point clouds, camera images, radar returns, and audio.
- Derived data, such as detections from the perception system or motion plans from the behavior system.
One approach is to keep only one category of data. Retaining only the derived data can still enable debugging of serious incidents, as long as the perception system can be trusted to provide a faithful representation of the raw sensor data. On the other hand, retaining only the raw sensor data makes the logs more useful for developing the mapping and perception system. An approximation of the derived data can be generated by running a replay simulator as needed, but it is challenging to reproduce the exact same outputs as those on the vehicle unless the AV software is fully deterministic.
Data retention decisions can also be made temporally. The key challenge here is high-recall classification of which time ranges in the log must be retained. For example, if a DMV-reportable collision occurs, the associated log data must never be discarded. These decisions can happen either on-device or in the cloud, but they must be made without uploading the full log to the cloud, since our bottleneck is the connection from the vehicle to the Internet.
Conclusion
The current trajectory for scaled autonomous driving would require desirable depot locations to include charging and Internet, making real estate acquisition challenging. There exist opportunities to reduce the additional requirements over time with the goal of making the problem closer to “rent a bunch of conveniently located parking lots.” While these are not traditionally considered autonomous driving problems, solving them will be key to unlocking the next phase of scaling.